車両の積載量を考慮した在庫引当て
こんなお悩みありませんか?
- 在庫の有無だけでなくトラックの積載量を考慮して倉庫を決める為、手間がかかっている
- 1日のトラック台数を考慮して出荷指示を物流会社に依頼しなければならない
- 追加の注文が来るたびに、全伝票の積載量を再チェックしなおしている
- 繁忙期と閑散期で積載量が異なる為、なるべく事前に把握しておきたい
注文を受けた案件に対して、正確な在庫の引当てをした上で、積載量から出荷可能なトラックの把握、追加のトラック手配交渉、顧客との納入日交渉など、受注手配業務の作業内容は多岐にわたります。ベテラン担当者でないと実施が困難という状況は発生していないでしょうか。配送計画を効率よく組む為には、出荷場所の決定、利用可能な在庫の引当て、積載可能量の把握を合理的に行える仕組みが必要です。
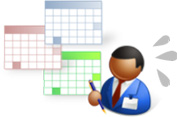
問題解決へのヒント
1.在庫引当て+積載量計算の判断方法
在庫の引当て業務と積載量の点検方法について、先行して積載量調整を行う場合は、在庫引当てが想定通り行われなかった場合に再度積載量調整が必要になります。逆に、在庫引当て完了後に積載量調整を行う場合は時間的にギリギリの状況が発生することもあり積載量オーバー時の調整が大変です。
在庫引当てと積載量点検は同時に行うことが合理的と言えますが、これを人間が行う場合、同時に2つの事を考慮しなければならず、高度な判断能力が必要になります。
しかしながら、在庫引当て業務+積載量点検の中でルール化可能な部分を調査・整理することで、自動的判断が可能になります。イレギュラーな場合だけ人間判断業務が必要になりますので、業務生産性が大きく向上することが見込まれます。
2.事前の積載量把握
仮に、1週間前に翌週の積載量が予測できたとしたら、予め必要なトラックの手配が可能です。
また、過去の出荷実績からの出荷予測数や受注残などが分かれば統計的に日別の出荷予測量から積載量が算出できます。
もちろん、予想外の需要が発生するケースもあります。その場合には、出荷タイミングを複数日に分散させるなどで調整するなどのルールを決めておくことで安定した出荷運用に繋がります。
3.積載量オーバー時の調整業務
受注に対して積載量がオーバーした場合、次のような対応が考えられます。
- 追加のトラックの手配可能可否の判断
- 翌日便への振替、振替対象の伝票の選定
- 他倉庫の在庫を参照し、利用可能であれば別拠点から直送出荷
- 顧客に対しての出荷数の変更調整
様々な対応がある中で、どの対応が適切かなどの判断は担当者の経験に任せられている事が多く見受けられます。過去の不足時の対応内容をデータ化することによって、システムから担当者に過去の判断結果を踏まえた対応方法を伝える事により判断業務の自動化が期待できます。
解決のポイント
- 在庫引当てと積載量の関係性を整理し、合理的な作業手順を整理することが必要
- 在庫欠品時、積載量オーバー時の作業ルールを決めることで繁忙期でも同じルールで運用できることが重要
- 事前に積載量の予測を行うことで、安定した配送を行える仕組みを構築する
関連する他のテーマ
関連する導入事例
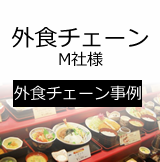
総合小売チェーン
総合小売業Z社様
生鮮輸入品における賞味期限別週間発注への引当・出荷調整業務を大幅に効率化
受注-在庫引当-出荷指示の一連の業務で半自動処理を実現
大手総合小売チェーンの生鮮品輸入業務を行うグループ会社M社様のご活用事例です。
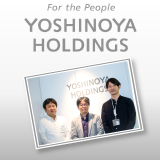
他業態外食チェーン
吉野家ホールディングス様
事業会社/業態のSCM・ロジスティクスシステムを統合・一元化し再構築、物流の共同管理・共同配送の基盤を構築し業務革新を推進
グループ事業会社として「吉野家」「はなまる」等があり、多店舗かつ複数の業態やブランドでの多角化事業を推進されている、吉野家ホールディングス様の活用事例です。